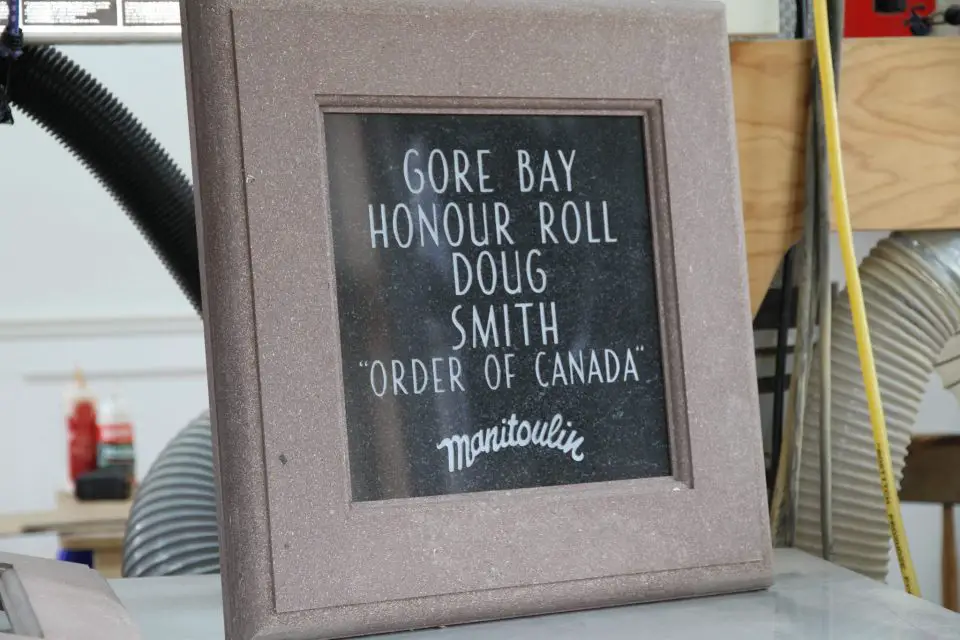
If you’ve got an outdoor wood project in mind, I’d like to suggest you make it with something other than wood. I’ll start with a story . . .
A number of years ago, two local heros were being celebrated in the little town near my home, and the commemoration included a couple of engraved granite plaques. Trouble was, the 1/2”-thick stone was too thin to be drilled and mounted directly onto a building. Without a frame of some kind to support the plaques and provide a mounting surface for bolts, the granite would crack. Wood was suggested as a frame material, but I didn’t like that.
Meeting the Outdoor “Wood” Challenge
If community volunteers ever neglected to maintain the wooden frames regularly over the years, it would weather, crack and turn grey. And is ratty wood any way to honour a person who’s received the Order of Canada? No, something completely maintenance-free was needed, and that’s what got me thinking about left-over Trex I’d stacked behind the shop.
Trex is one of a handful of non-hollow composite materials, made by various companies from a 50/50 blend of recycled plastic and wood fibers. The feedstock is typically plastic shopping bags and old wooden shipping pallets. The granite-like appearance of Trex proved to be a perfect complement to the actual granite of the engraved plaques, and I know from experience that composites weather well. Even after a decade of sun and weather, the only change is a slight fading of colour.
But as durable as it is, it didn’t take long for me to discover that the slight warps and cups in each composite board would make any kind of fine craftsmanship impossible, at least until these issues were fixed, that is. Though irrelevant in a deck, this distortion is a deal breaker in finer work. But then I discovered something new about composites.
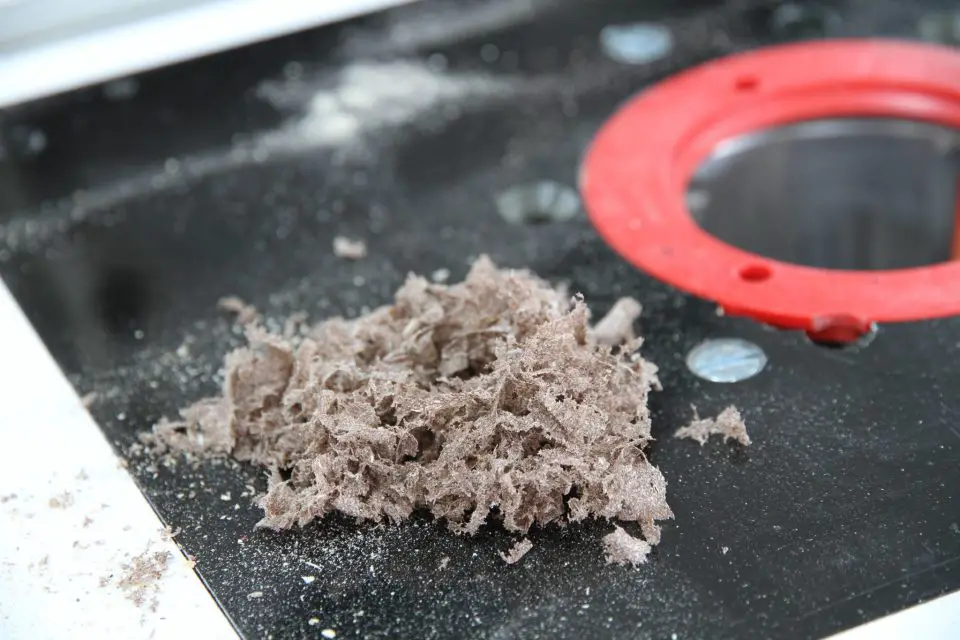
Working With Composites as Wood
The same jointing, planing and routing operations that create the kind of smooth, flat, square wooden boards necessary for cabinets, tables and shelves also work on composites. In fact, they work even better than on wood. Composites are so stable, consistent and machineable, that they mill like a dream. There’s no melting of the plastic component while cutting, planing or routing, and it doesn’t seem to dull tools any faster than wood. After rough-cutting composite boards to length and width, the jointer did an astonishing job creating flat surfaces and square edges on formerly concave Trex boards. My thickness planer also milled the blanks down to perfect final thickness, though I was still left with a big question. How can I securely join outdoor materials that are 50% plastic in a high-stakes situation?
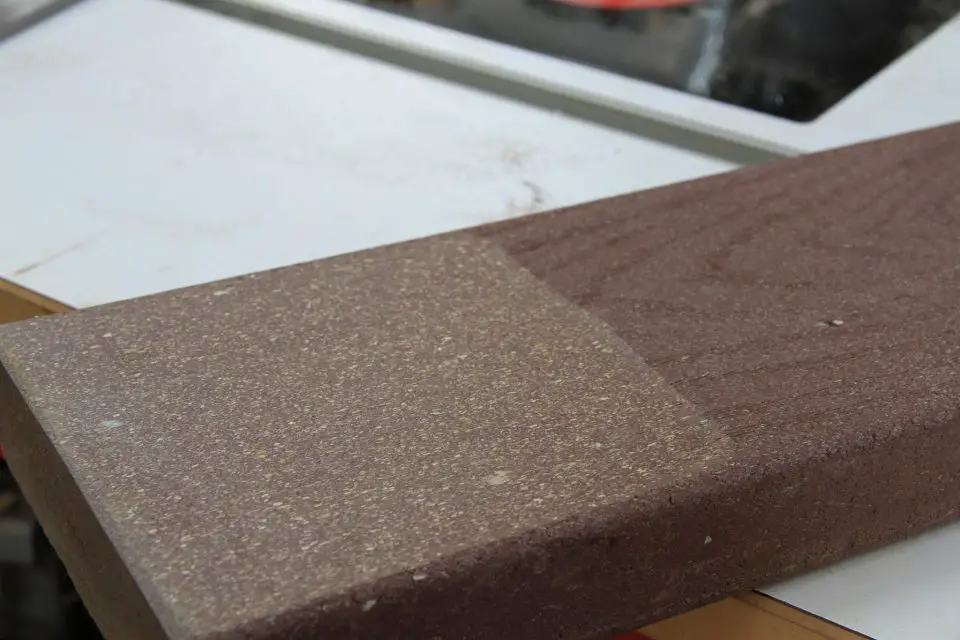
Joining Composite Parts
I knew that ordinary wood glue would never hold, but what about polyurethane adhesives? How about PVC cement? Construction adhesive? In the end, after trying several options, I settled on epoxy because it worked so well in my tests. I originally tried a five-minute formulation, and though it holds composite securely, I needed more assembly time. A four-hour epoxy proved perfect, and that’s what I used on the frames here. Just give it at least two or three days to cure. Try to sand off excess glue any sooner than that and it’ll clog up your abrasives way too fast.
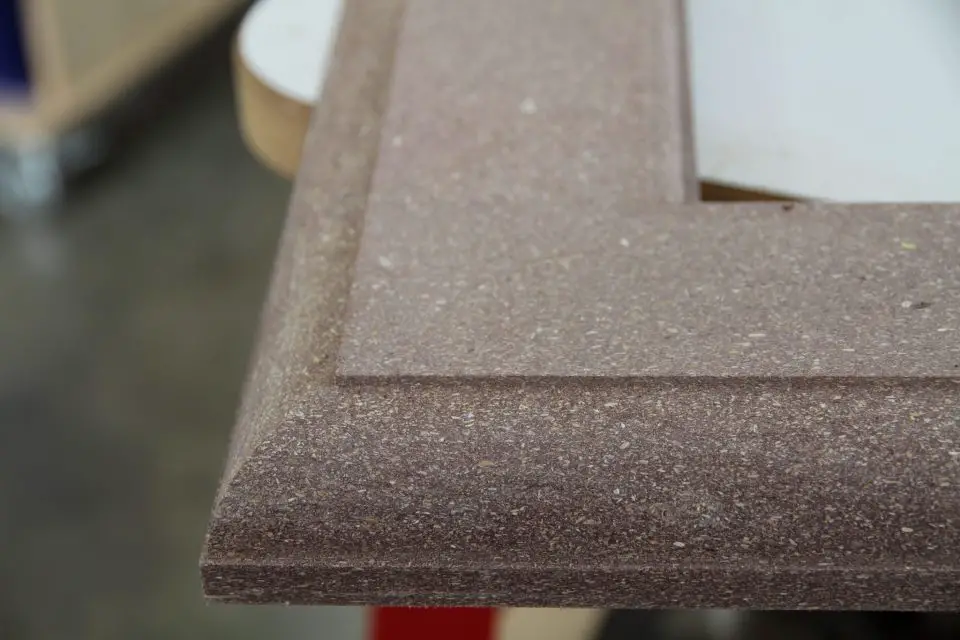
The cope-and-stile joinery I used for my frames needed nothing more than glue for a secure joint. My tests showed that for sure. Even bashing assembled test joints with a hammer could not break them apart. If your projects include butt joints and mitres, you’ll need to add some kind of mechanically interlocking connection like dowels or biscuits. Screw joints work fine for low-stress situations, and are easy to hide using tapered plugs made out of composite.
Once you realize that composites can be jointed, planed, milled and glued with precision, it becomes possible to build weather-tough display frames, boxes, birdhouses, cabinets, work surfaces and even fine outdoor furniture. Of course composites will never take the place of real wood, but they’re a pretty good alternative when water, weather and sun are working against you.
Tapered Composite Plugs
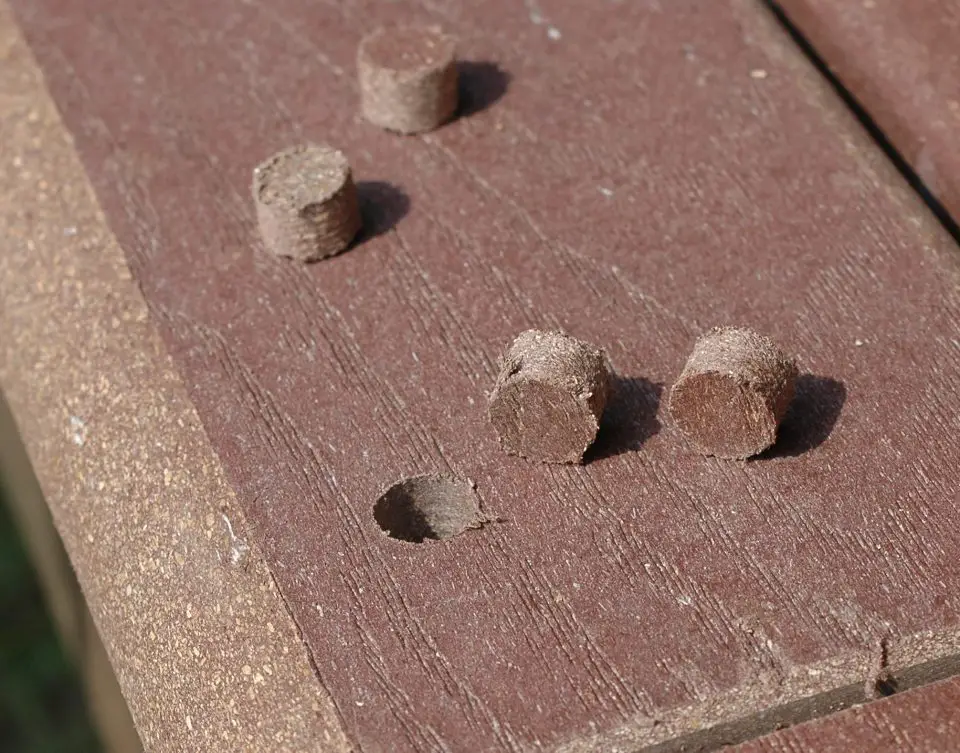
You can make your own shop-cut tapered plugs from composite just like with regular wood. They’re perfect for concealing counterbored screws and blend seamlessly with neighbouring surfaces. Chuck a tapered plug cutter into your drill press, then place a piece of composite underneath that’s about 1/16” thicker than the length of plugs you’ll be making.
Plunge the spinning cutter down into the composite until you’ve made all the plugs you need, then switch off the machine, pick up the block, and break the plugs out with your fingers as needed. Although regular wood glue doesn’t bond composites strongly enough for use on structural joints, it does hold tapered wood plugs effectively in their holes. Single-part glue is also a lot handier to use than two-part epoxy that needs mixing. Weatherproof wood glue also endures well outdoors.