A number of years ago I was driving through small town Canada and something unusual caught my eye. Stacked next to a tall, elegant waterfront building under construction was a tarped pile of building products with the name “Formtech’”printed on the side. I recognized the company as a Canadian manufacturer of insulated concrete forms (ICFs), and that’s when it all clicked. I’d heard about ICF technology beginning to make its way into large, commercial projects like this, but had never seen it before in person. Now it’s happening.
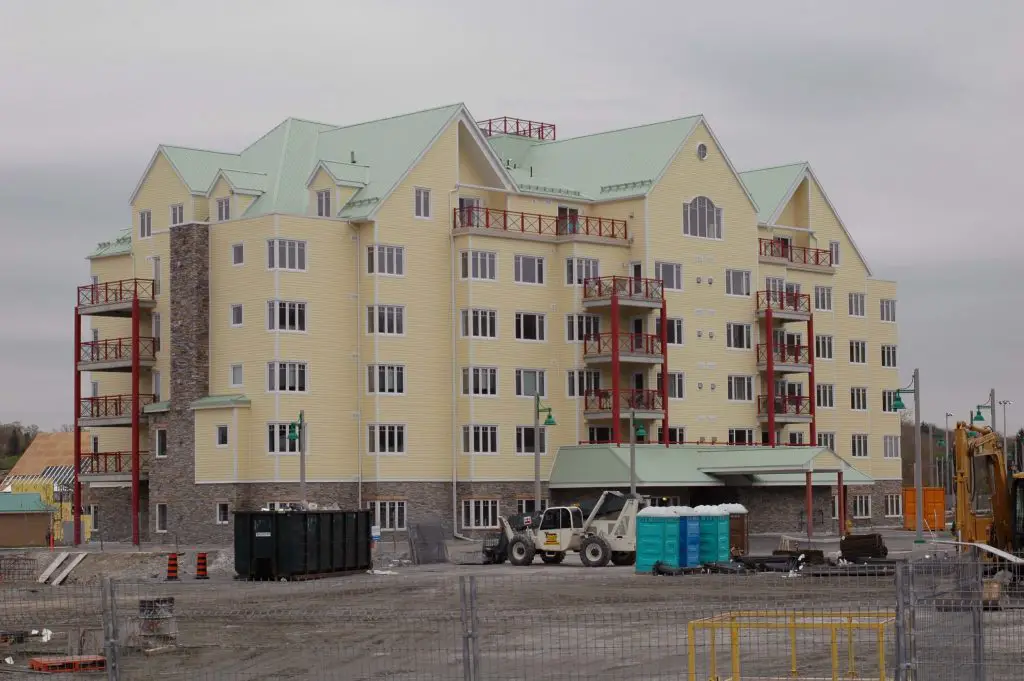
The building that caught my eye is the Ditchburn Condo, shown above, part of a $200 Million waterfront development called Muskoka Wharf. And the fact that ICFs are now towering there six stories high is a landmark gain in the advancement of this technology. This application also has something to offer you as an quality-conscious homeowner interested in building a new home or putting up an addition.
ICFs are a building system that combines the energy efficiency of rigid foam sheets with the structural strength and soundproofing qualities of concrete. They’re made by a number of companies these days, and all operate on the same basic principle. Foam takes the place of wooden forms, remaining in place after the concrete has cured. This creates a continuous layer of insulation on both interior and exterior wall surfaces, with a large thermal mass sandwiched in between.
When ICFs first arrived on the Canadian building scene back in the 1980s, they were only used for basements. They still work well in that application. ICFs yield a foundation that’s prime for turning into a finished rec room or basement rental suite later on, and that’s why ICF technology began catching on in a big way. But if warm concrete walls are good below ground, why not above? That realization slowly led to the use of ICFs for above-ground walls in homes and cottages. This is common now.
The Ditchburn Condo at Muskoka Wharf is one step in the upward movement of ICF building systems, and with it comes some energy analysis stats that say a lot, even for people thinking of building small. I predict we’ll see more multi-story ICFs going up, plus lots of single family dwellings and cottages.
Besides offering a high level of fire resistance and sound exclusion, the ICF construction at the Ditchburn Condo made the building eligible for a federal government campaign called the Commercial Building Incentive Program (CBIP). This awarded up to $60,000 towards the design costs of commercial buildings that are able to save at least 25% of the energy used by similar buildings constructed to the latest code standards. Typical ICF buildings save as much as 70% on heating and cooling, so eligibility was no problem. This translates into ongoing savings for Ditchburn residents, too.
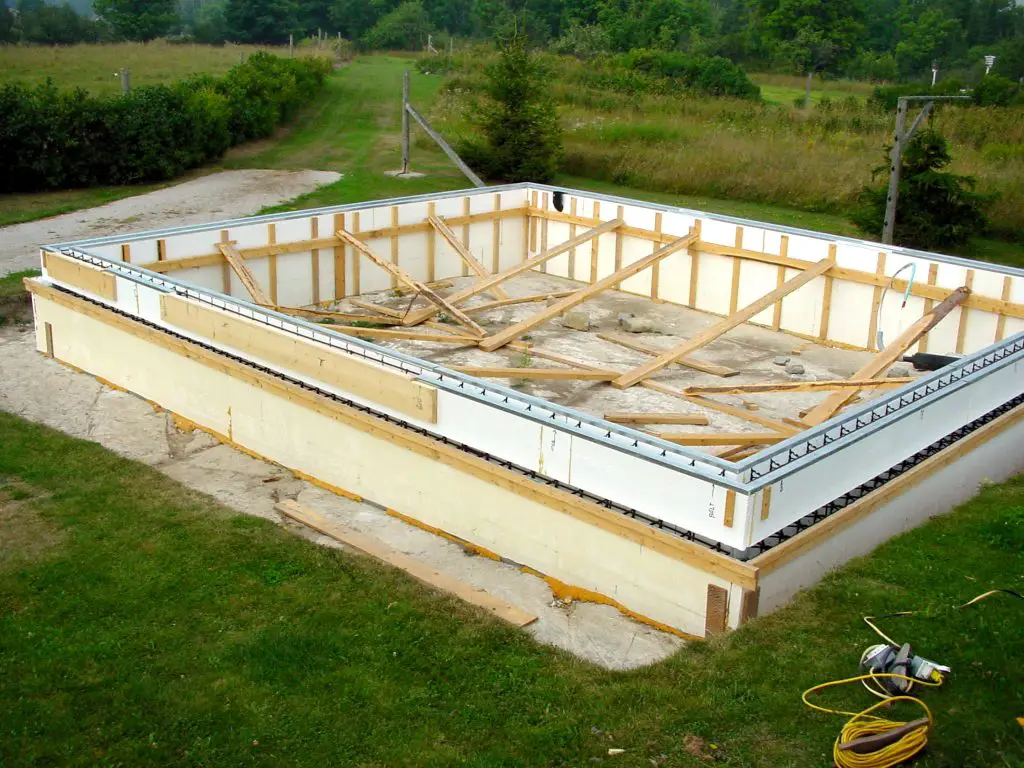
I’ve worked with ICFs personally on small projects, and plan to work with them again. The forms are light and a lot easier to assemble than plywood forms. ICFs are also terrific for rocky, cottage country building sites. It’s quite easy to scribe and cut the foam forms so they follow undulating bedrock closely. There’s no neater, easier way to build a foundation on rock. Below you can see one side of a foundation I built, with the bottom edges of the foam cut to fit the undulating bedrock.
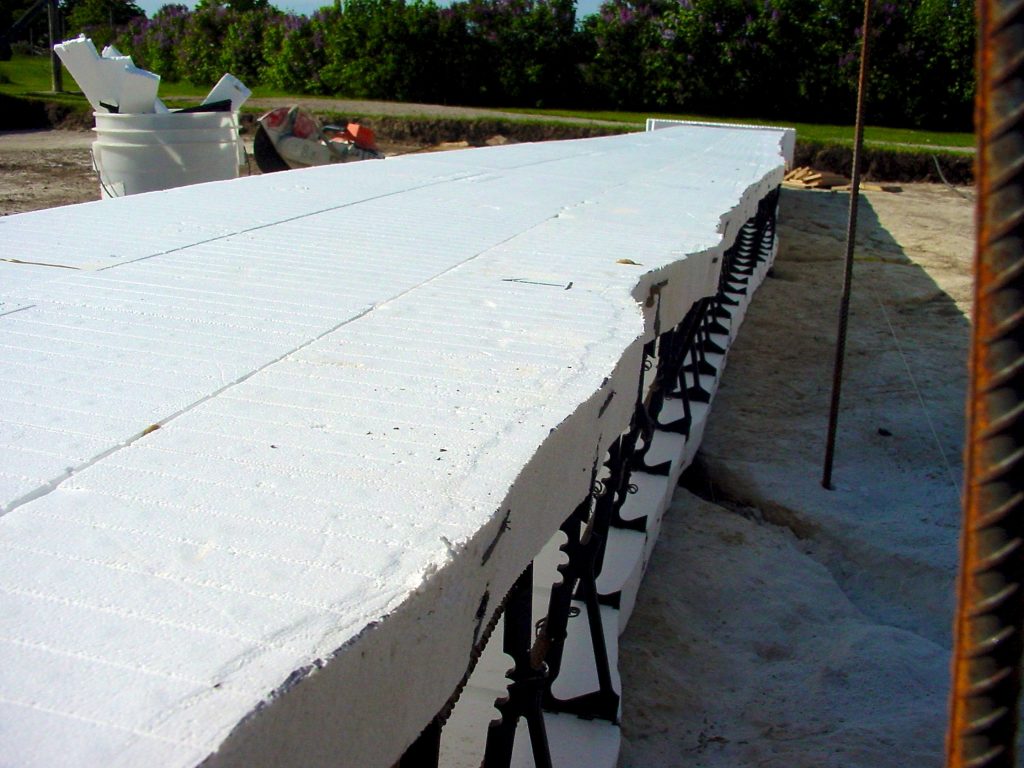
As you’re planning an ICF project though, you must take into account the need for concrete handling equipment around the building site, especially if your building is higher than one story. Also, it’s not very easy to alter window and door locations after an ICF building is up. Get these details correct before proceeding, of course.
But these drawbacks aside, I’m glad ICFs are here. They’ve proven themselves worthy from the ground up over the last three decades. In a world with high energy prices and rising consumer expectations, ICFs are one example of leading-edge building technologies that are making a difference.
Did you find this article useful? I hope so. Please consider joining other visitors who help cover my out-of-pocket expenses to produce content like this and publish it. Clicking the ‘buy me a coffee” button below offers a fast, easy and safe way to make a contribution. A big thank you to everyone helping out in this way.