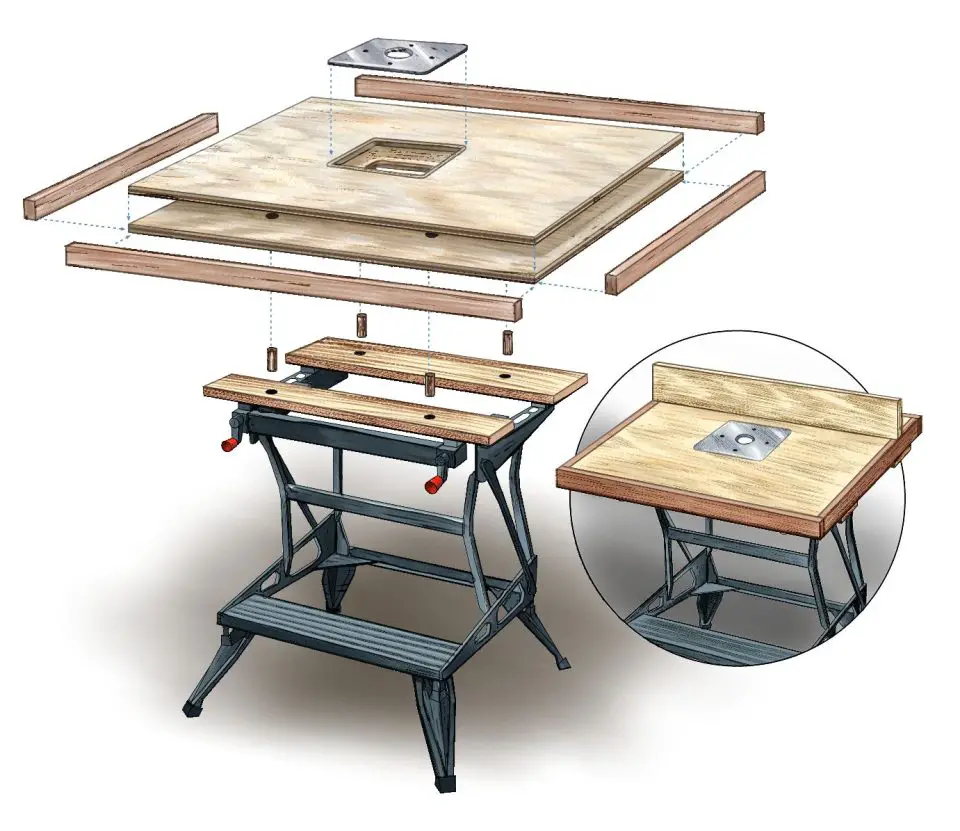
More than one old-timer I know tells how new carpenters used to be judged on the job by their ability to build a sawhorse. If they could deal successfully with the required angles and joints of a sawhorse, creating something solid and useful for the rest of the crew to use and scrutinize, then they could probably frame a roof or put together a wall. Back then sawhorses were four-legged wooden resumes.
But as the building world has become more of a plug-and-play proposition, site-built sawhorses have pretty much taken a back seat to ready-made alternatives. Sawhorses are still useful, and I currently have about a dozen that I’ve built and use. That said, it’s hard to argue with the performance of some of the new alternatives. Here’s a look at two portable workstations that have earned a regular place in my life.
Triton Super Jaws

As you can see, the 45 lbs. Super Jaws has no trouble supporting this old-time wooden sawhorse solidly. Despite unbalanced loads like this, the three-legged design remains stable on uneven surfaces. That makes it useful for planing doors, supporting stationary machines bolted to interchangeable wooden bases, and for cutting materials with hand-held saws. I use my Super Jaws most often for metal fabrication and welding. With practice you can fold the unit up in about half a minute when you’re done work. The yellow and brown epoxy-powder coating is tougher than paint, and the corrosion-resistant nuts and bolts really are rust-proof.
Clamping action happens via a foot-operated pedal. It works through a mechanism generating anything from light pressure to more than 2000 lbs. of clamping force at the urethane-padded jaw faces. Operation is faster than thread-driven mechanisms, with jaws locking automatically as foot-pressure is released.
I did have some mechanical trouble with the locking system on one of several Super Jaws I own, but repaired it easily on-site with a centre-punch and hammer. It’s been completely reliable since then. Besides the fact that the jaws open as wide as 35 inches, operation of the tool is quick and easy because the design makes use of both your upper and lower body, something no other workstation I’ve seen does as well. You’ll find Super Jaws at Amazon.
Workmate Router Table
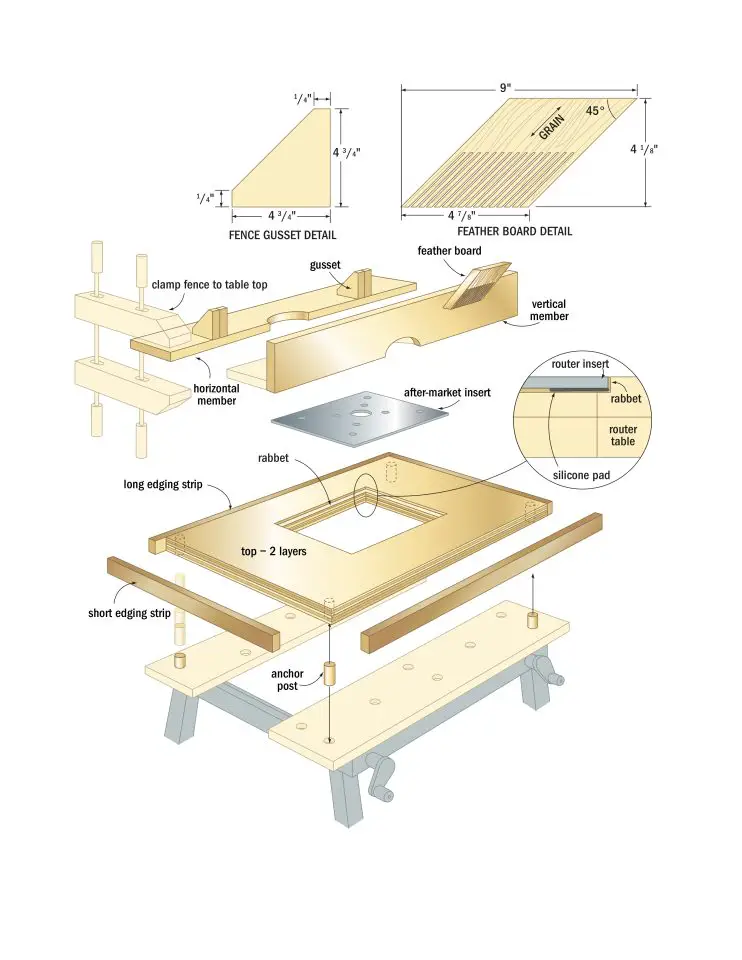
Do you have a router? The shop-built idea above helps any router reach full potential. It supports the router for operations like milling molding, rounding the edges of small parts, and cutting dado and rabbet grooves. But full-size router tables can be heavy, awkward to transport and expensive. That’s where my home made router table top comes in.
A double-layer of 3/4-inch birch plywood makes a great router table top, especially when it’s edged with hardwood. It’s hefty enough to be solid, and I made it to be clamped into my portable Workmate. The plywood top is thick enough to secure the 3/4-inch diameter anchor dowels set in to the bottom face. These dowels extend downwards and interlock with holes in the Workmate top, securing the router table surface by tightening or loosening the jaws. A plastic base plate sits in rabbet grooves in the router table top, with the router suspended from it. Since gravity holds the machine in place, just lift the router out whenever you want to use it free-hand. I hardly ever remove the over-sized router table base plate since it’s a least as handy as the smaller stock base plate for free-hand routing.
The right workstation makes a huge difference in the speed, success and quality of what you make or fix or build. Get the workstation right and everything else falls more easily into place. Want to build my own design of sawhorse? Click here for downloadable plans and a video tutorial.